Banana fiber processing and weaving
The extraction of the natural fiber from the plant required certain care to avoid damage.
In the present experiments, initially, the banana plant sections were cut from the main stem of the plant and then rolled lightly to remove the excess moisture. Impurities in the rolled fibers such as pigments, broken fibers, coating of cellulose, etc,… were removed manually by menas of a comb, and then the fibres were cleaned and dried. This mechanical and manual extraction of banana fibres was tedious, time-consuming, and caused damage to the fibre. Consequently, this type of technique cannot be recommended for industrial applications.
A special machine was designed and developed for the extraction of banana fibres in a mechanically automated manner. It consisted mainly of two horizontal beams whereby a carriage with an attached and specially designed comb, could move back and forth. The fibre extraction using this technique could be performed simply by placing a cleaned part of the banana stem on the fixed platform of the machine, and clamped at the ends by jaws. This eliminated relative movement of the stem and avoided premature breakage of the fibres. This was followed by cleaning and drying of the fibres in a chamber at 20oC for three hours. This fibres were then labeled and ready for lamination process.After extraction of fibre, weaving is done in the looms as per normal process like any other material.
The processes for making yarn from banana fibers vary from region to region. Most popular methods among these are those followed in Japan and Nepal.
Japanese Method
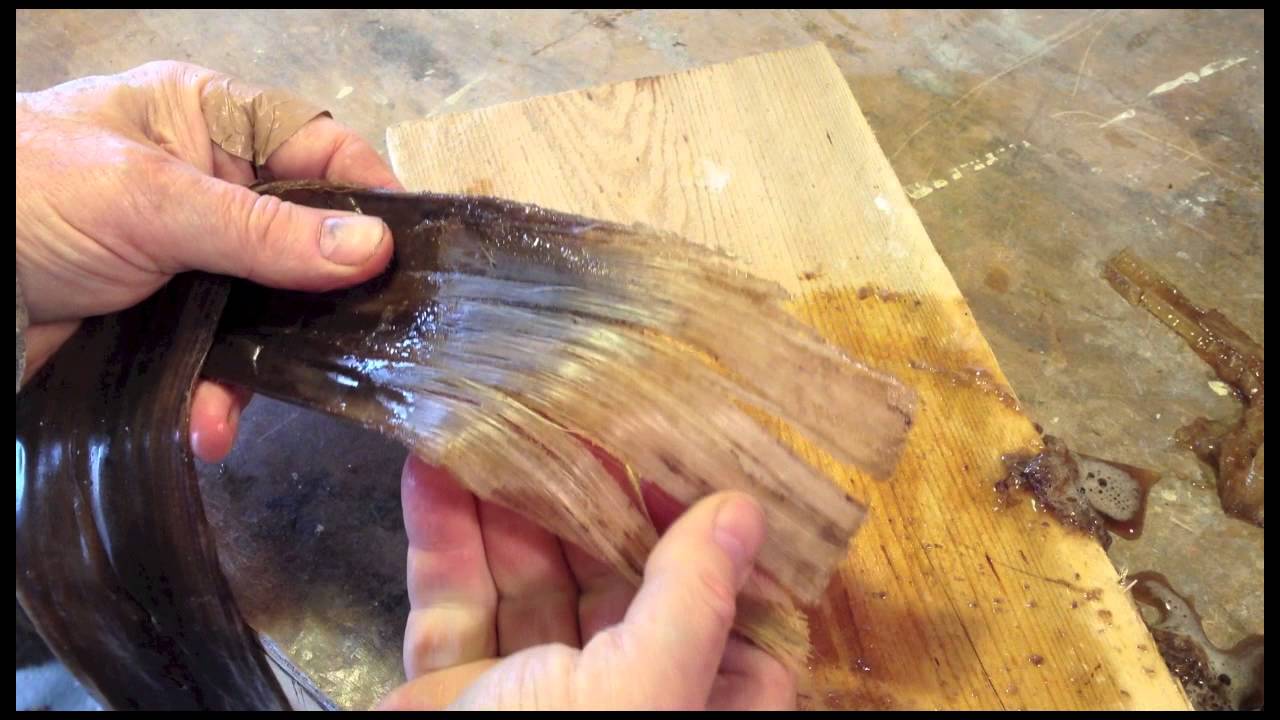
The cultivation of banana for clothing and other household use in Japan dates back to the 13th century. In the Japanese method of making banana fiber, the care is taken right from the stage of plant cultivation. The leaves and shoots of the banana plant are pruned periodically to ensure their softness. The harvested shoots are first boiled in lye to prepare the fibers for making the yarn. These banana shoots give away fibers having varying degrees of softness. This further results in yarns and textiles with differing qualities that can be used for specific purposes. The outermost fibers of the shoots are the coarsest ones. They are, therefore, more suitable for making such home furnishings as tablecloths. The softest part is the innermost part that gives soft fibers which are widely used for making kimono and kamishimo, the traditional Japanese apparels. The banana cloth-making process is a lengthy one and all the steps are performed by hand.
Nepalese Method

In Nepal, the trunk of the banana plant is harvested instead of the shoots. Small pieces of these trunks are put through a softening process for mechanical extraction of the fibers, and then bleaching, and drying. The fiber obtained thus has an appearance similar to silk which has become popular as banana silk fiber yarn. This fiber is refined, processed and skeined mostly by the Nepalese women. Only the aged bark or the decaying outer layers of the banana plant are harvested and soaked in water to quicken the natural process. When all the chlorophyll is dissolved, only the cellulose fibers remain. They are extruded into pulp so that they may become suitable for spinning into yarn. The yarn is then hand-dyed. They have a high textural quality similar to silk and as such employed in making high-end rugs. These traditional rugs are woven by hand-knotted methods again by the women of Nepal.
You may also be interested in